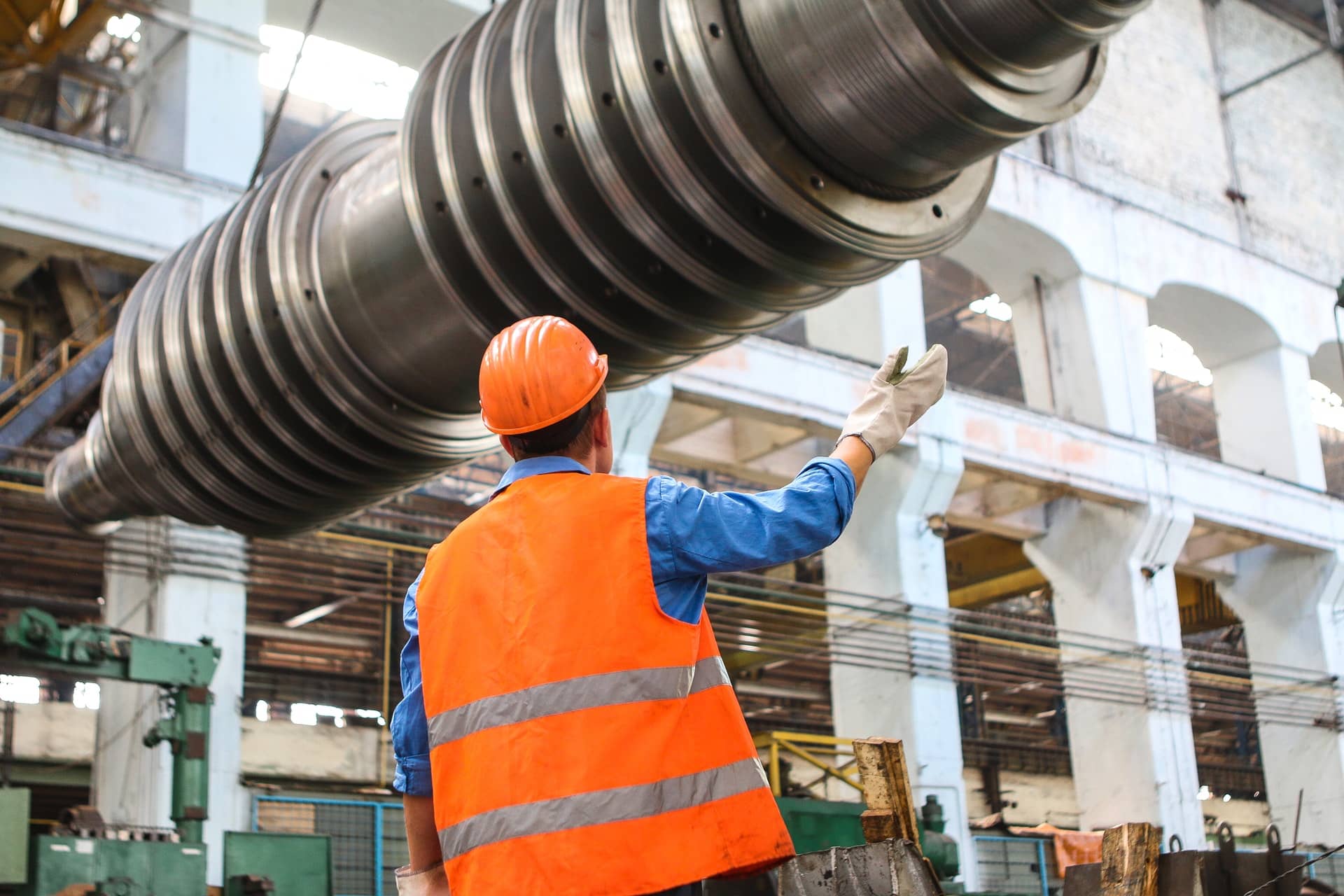
Reliability Centered Maintenance (RCM)
What is RCM?
The reliability centered maintenance (RCM) methodology is used to develop or optimize the maintenance program for physical assets. The final outcome of RCM is the implementation of a strategy to help companies ensure that any physical asset, system or process continues to do whatever its users want it to do in its present Operating Context. Increasing equipment reliability is key and can result in any number of positive outcomes; namely, reduced downtime, improved safety, increased productivity, and reduced overall maintenance costs.
There are others who know about RCM. At Aladon, we know what RCM is about.
Understand RCM2™ vs. RCM3™
Compare RCM2 to RCM3 with this progression table that illustrates the extended capabilities of RCM3. Click to view it here. RCM3 is now the new standard for how organizations manage their operational risks and improve asset integrity.
- RCM3 exceeds SAE standards and broadens RCM2 capability to align with more recent and internationally accepted ISO Management Systems (ISO 55001 and ISO 31000).
- RCM3 is fully integrated with other Business Risk Management Systems like Root Cause Failure Analysis, Risk- Centered Spares (RCS) and HAZOP.
- RCM3 is no longer just another initiative, but a mainstream business risk management process that could become the most important management system for improving Process Safety and Asset Integrity.
- Our new risk-based methodology is the only process companies need to maintain and optimize all their assets (rotating and static).
- RCM3 is the best response to the challenges and expectations brought by the Fourth Generation Maintenance.
- RCM3 is now the process industry’s most advanced method for managing maintenance and operations to control costs and boost overall productivity.
Compare RCM2 to RCM3 with this progression table that illustrates the extended capabilities of RCM3. Click to view it here.
Looking for more information? Read below about RCM2 or RCM3.
4 Principles That Guide an Effective RCM Program
- Preserving system functions as the primary objective.
- Identifying failure modes that can impact system functions.
- Prioritizing the failure modes.
- Finding solutions to manage the likelihood of occurrence or the consequences of the failure modes (or both through evaluating the inherent risk associated with owning and operating assets).
The RCM process identifies the functions of the assets that are most vital and then seeks to maximize failure management strategies so that system failures are eliminated or kept at a minimum and equipment reliability is increased. It entails asking seven questions about the asset or system under review.
RCM: Seven Basic Questions About an Asset
Aladon’s founder, John Moubray, developed and trademarked the rigorous and robust seven question process called RCM2™. The seven questions follow the logic of the methodology that originated from the work by Nowlan and Heap in their 1978 report called “Reliability-centered Maintenance (RCM).” These questions are:
- What are the functions and associated performance standards of the asset in its present operating context?
- In what ways does it fail to fulfill its functions?
- What causes each functional failure?
- What happens when each failure occurs?
- In what way does each failure matter?
- What can be done to predict or prevent each failure?
- What should be done if a suitable proactive task cannot be found?
The RCM process provides powerful rules for deciding whether any failure management strategy is technically appropriate and worth doing. It also provides precise criteria for deciding how often routine tasks should be done.
Benefits of RCM
Aladon’s RCM-based Training and Advisory Services are offered exclusively through our world-class global community of reliability professionals, aimed at firms looking for an integrative Enterprise Resource Management (ERM) approach, that means enhanced system-wide insight of the asset life-cycle, plus an unmatched understanding of how maintenance and operations work together for greater integration. Building operational integrity is easier than ever through our world-class training and services.
Increased Efficiency
- Enhance compliance activities
- Reduce business interruptions
- Increase asset utilization
- Increase uptime
Reduced Costs
- Manage lifecycle costs
- Optimize maintenance and inspection intervals
- Prevent unwanted events
- Make data driven decisions
Improved Productivity
- Optimize your assets
- Reduce operating costs
- Improve sustainable reliability
- Improve customer satisfaction
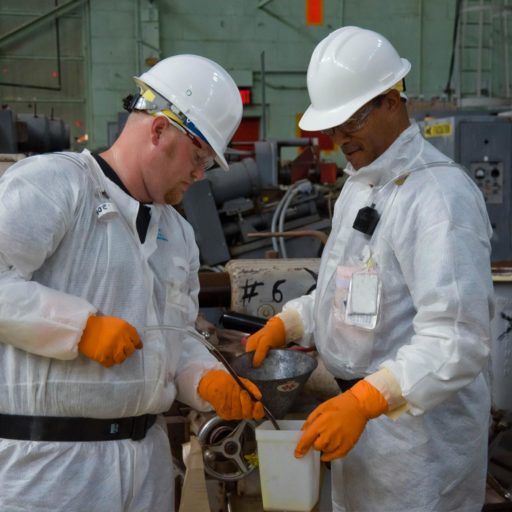
RCM2™/RCMII™
Our founder, John Moubray, developed a profound and unique way to perform reliability centered maintenance analyses. RCM2 (RCMII) was developed from the original work done by Nowlan and Heap. One of the features of RCM2 that distinguishes it from other interpretations of the RCM philosophy is the cross-functional groups of users and maintainers that perform the analyses. After training, these analysis teams apply the process to their assets to produce the most cost-effective asset reliability programs.
RCM2 identifies the most critical assets of a company and how best to optimize its maintenance strategies to reduce system failures. Any assets that are likely to fail or have a large consequence if they do—are considered your most critical assets.
In essence, users may expect a whole host of different things from their assets, depending on certain performance parameters, such as output, throughput, speed, range and carrying capacity. Where relevant, the RCM2 process defines what users want in terms of risk (safety and environmental integrity), quality (precision, accuracy, consistency and stability), control, comfort, containment, economy, customer service and so on.
The RCM2 process identifies the ways in which the system can fail to live up to these expectations (failed states), followed by an FMECA (failure modes, effects and criticality analysis), to identify all the events which are reasonably likely to cause each failed state.
Effective techniques are then adopted to minimize the possibility of failure and improve the reliability of the facility as a whole. The RCM2 process provides powerful rules for deciding the effectiveness of any failure management policy. It also provides precise criteria for deciding how often routine tasks should be done to better boost reliability.
RCM2 completely transforms the view that any organization has of its physical assets. Not only does it revolutionize views about maintenance and how it can work together with operations, but it also leads to a far broader and deeper understanding about how things work in general.
As a result, assets become more reliable because they are better maintained, plus operators are less likely to do things which cause their assets to fail. A better understanding of how systems work also means that operators are far more likely to react quickly, confidently and correctly when things do go wrong—a capability which is quite literally priceless, especially in complex, hazardous, tightly coupled facilities.
One of the greatest strengths of RCM2 is that it recognizes that the consequences of failures are far more important than their technical characteristics. In fact, it recognizes that the only reason for doing any kind of proactive maintenance is not to avoid failures per se, but to avoid or at least to reduce the consequences of failure.
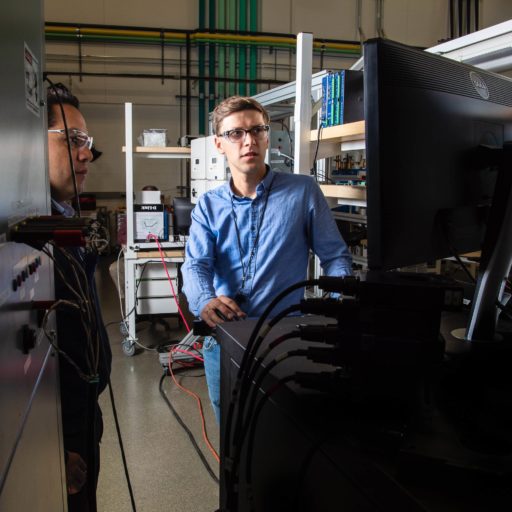
RCM3™
Aladon developed RCM3 as an enhanced version of RCM2, the trademark methodology for Aladon.
RCM3 is our risk-based RCM. Everything we’ve learned over many years of researching and testing Reliability Centered Maintenance has gone into improving and enhancing our RCM methodology. And, we keep learning — everything we do, each passing milestone makes RCM3 even better.
RCM3 exceeds SAE standards and broadens RCM2 capability to align with more recent and internationally accepted ISO Management Systems (ISO 55001 and ISO 31000). Additionally, RCM3 is fully integrated with other Business Risk Management Systems like Root Cause Failure Analysis (RCFA), Risk Centered Spares (RCS) and HAZOP.
RCM3 is no longer just another initiative, but a mainstream business risk management process that could become the most important management system for improving Process Safety and Asset Integrity. Our new risk-based methodology is the only process companies need to maintain and optimize all their assets (rotating and static).
RCM3 is the best response to the challenges and expectations brought by the Fourth Generation Maintenance.
RCM3 is now the process industry’s most advanced method for managing maintenance and operations to control costs and boost overall productivity. Our aim is to continue to explore new technologies and trends working with our global Network and Technology Partners to lead the world with our world class training courses and robust methodologies.
How Aladon Implements RCM
When it comes to RCM, there is a reason that hundreds of organizations around the world choose Aladon. We have a track record of over 30 years of implementing RCM in every industry on six continents. Because we recognize that implementation is the biggest challenge to the RCM methodology, we offer a step-by-step approach, with a go/no go decision at every stage. The initial process of analysis is the easy part, but it’s in the implementation of RCM that sets Aladon apart.
Implementing RCM often requires changes to existing work processes and tasks that require time and resources to complete. That’s why our approach is to mentor clients through the complete RCM process (planning, scoping, preparation and training, performing, review and audit, implementation and continuous improvement), rather than merely train them. While we know that the benefits of RCM in every industry outweigh the challenges, we nonetheless offer our clients opportunities to opt out of the process at every stage. This saves them from making large resource commitments and investments up front.
Following is our systematic approach that has proven our methodology with hundreds of clients throughout the world in every industry:
- Executive Overview: From the start, we spend one day reviewing the RCM process and methodology to an organization’s stakeholders, including: the C-suite, managers, union leaders, program sponsors or anyone who has oversight. The executive overview is focused on the benefits of an RCM-based improvement program and the requirements for successful implementation. From there, the company can decide if they want to proceed.
- Introductory Training: We offer a three-day course with a designated team from the organization, including: engineers, operation managers, maintenance managers, union leaders and subject matter experts. After that, we again offer the organization a go/no go decision.
- Advanced Facilitator Classroom Training: If the organization decides to continue, a select group from the introductory training course joins a 10-day facilitator training program. The facilitator program allows the organization to implement RCM on their own assets using their own people.
- Facilitator Coaching and Mentoring: We assist a select group of the participants from the classroom training group through a pilot project where they analyze equipment they own. This is an onsite process and our experience has shown that the average facilitator delegate will need approximately three weeks of mentoring to be able to work independently. The mentoring and coaching includes activities such as asset prioritization, developing a risk framework, selecting equipment and scoping the analyses, planning the review meetings and audit, and ensuring all the resources are aligned for implementation. Once the classroom training and mentoring period is complete, we perform an onsite evaluation where we determine who has mastered the rigorous RCM3 process and is ready to become a facilitator.
- Audit, Prepare and Implement results: Together with the facilitator and asset owners, we audit and assist in the implementation of the RCM recommendations. This includes writing detail job plans, developing performance indicators and failed states, optimization of the PM routes, CM prioritization and spare part recommendations.
- Execution and Continuous Improvement: Facilitators work to execute the program with our support, which includes training and mentoring to ensure the team applies the methodology according to our recommendations. Recommendations must be implemented and reviewed periodically.
In addition to this well-developed process, our practitioners typically have at least 15 years of experience. We assign each organization a certified network member with direct experience in their particular industry. The process of RCM is the same in every industry, but we know that industry expertise ensures better results.
There are others who know about RCM. At Aladon, we know what RCM is about.