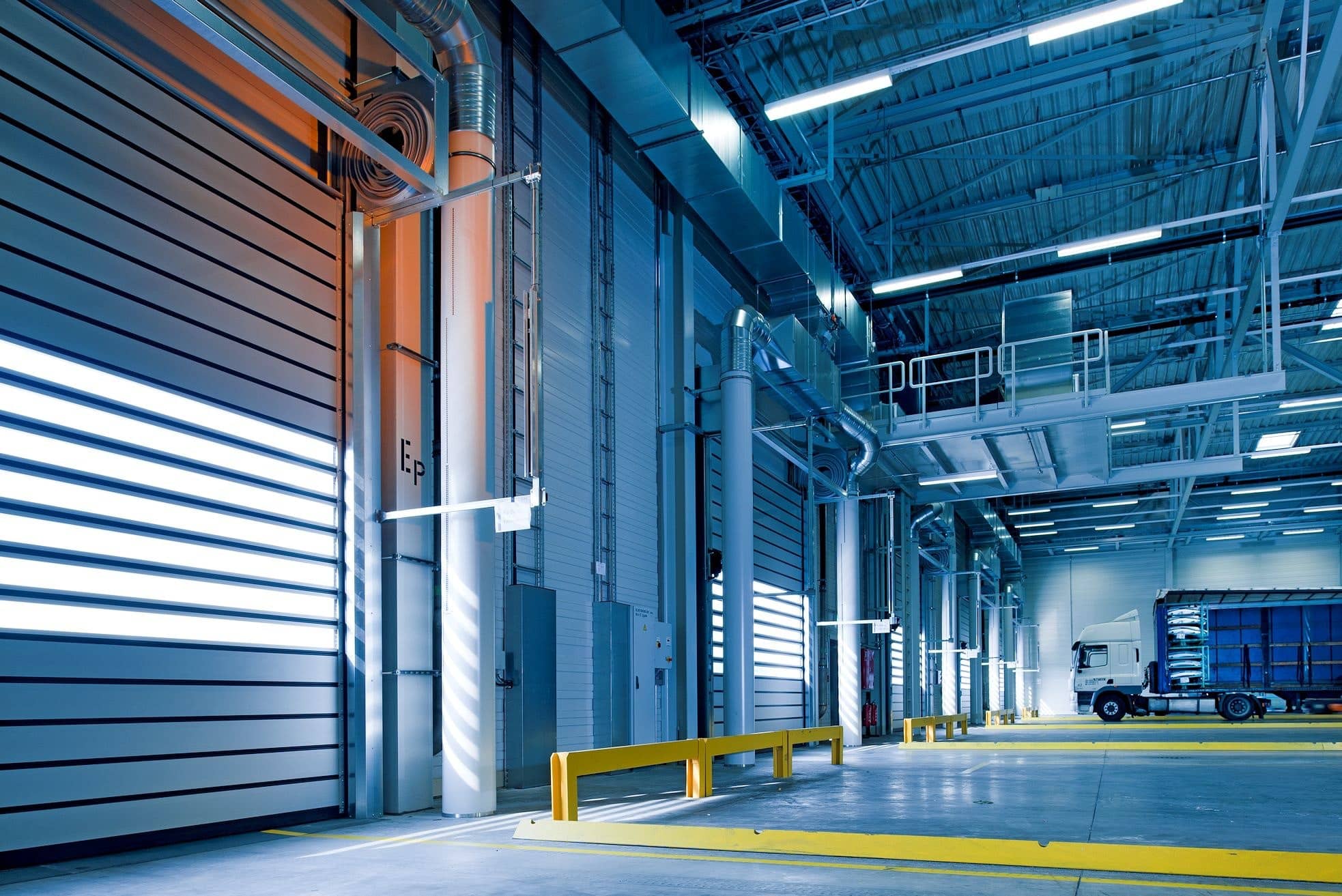
RCM3™
The Only Process Needed for All Your Assets
There are others who know about RCM. At Aladon, we know what RCM is about.
Everything we’ve learned over many years of researching and testing Reliability Centered Maintenance has gone into improving and enhancing our RCM methodology. Aladon developed RCM3 as an enhanced version of RCM2™, the trademark methodology for Aladon.
Your organization’s success is limited by how well equipped you are to implement RCM3 to its fullest. That’s why when you work with Aladon, we support your organization for the long haul. The majority of RCM initiatives fail, but the organizations that adopt Aladon’s methodologies and stay with us over time prove to successfully transition from reactive maintenance to proactive maintenance. The effect of correctly implementing RCM3 technology can be tremendous, saving money, time, the environment and even lives.
Benefits of RCM3
- Increase reliability, availability and productivity
- Optimize maintenance and avoid unnecessary costs
- Boost safety awareness and environmental integrity
- Generate a better understanding of equipment behavior
- Share information across the entire organization
- Exceeds SAE standards and broadens RCM2 capability to align with more recent and internationally accepted ISO Management Systems (ISO 55001 and ISO 31000)
- Integrates with other Business Risk Management Systems
RCM3 is no longer just another initiative, but a mainstream business risk management process that could become the most important management system for improving Process Safety and Asset Integrity. Our new risk-based methodology is the only process companies need to maintain and optimize all their assets (rotating and static).
Highlights of the new textbook include:
- Strengthening the robust foundational RCM principles
- An explanation of RCM3 process at length with new practical examples
- How to apply RCM3 and how the assets should be selected
- Background information about how maintenance has changed over four generations and how the requirements of Industry 4.0 places additional pressure on maintenance departments
- How to adhere to ISO Standards for Physical Asset Management and Risk Management (ISO 55001 & ISO 31000) and how RCM3 puts asset management mainstream with other business management processes
- Information about the actuarial analysis and failure data and how proper use of technology advances reliability
- Updated approach for testing and handling of protective devices
- Maintenance in the age of the fourth industrial revolution (Industry 4.0) and its challenges
The RCM3 book is excellent material to read and kept me occupied for last month or so. I was extremely enjoying that process. It is thorough and very easy to understand and follow. The binder you had given us last year is also super user-friendly and helps with brushing through the concepts. I will highly recommend my peers read this book. Years and years of hard work is thoroughly visible in the content of the book and material.
Hit Your Targets with RCM3
RCM3 identifies the most critical assets of a company and how best to optimize its maintenance strategies to reduce system failures. Any assets that are likely to fail or have a large consequence if they do—are considered your most critical assets. Having this information and a plan at your fingertips is key to knowing everything that can go wrong with your assets and still be able to sleep at night.
In essence, users may expect a whole host of different things from their assets, depending on certain performance parameters, such as output, throughput, speed, range and carrying capacity. Where relevant, the RCM3 process defines what users want in terms of risk (safety and environmental integrity), quality (precision, accuracy, consistency and stability), control, comfort, containment, economy, customer service and so on.
The RCM3 process identifies the ways in which the system can fail to live up to these expectations (failed states), followed by an FMECA (failure modes, effects and criticality analysis), to identify all the events which are reasonably likely to cause each failed state.
Effective techniques are then adopted to minimize the possibility of failure and improve the reliability of the facility as a whole. The RCM3 process provides powerful rules for deciding the effectiveness of any failure management policy. It also provides precise criteria for deciding how often routine tasks should be done to better boost reliability.
Gaining a Deeper Understanding
RCM3 completely transforms the view that any organization has of its physical assets. Not only does it revolutionize views about maintenance and how it can work together with operations, but it also leads to a far broader and deeper understanding about how things work in general.
As a result, assets become more reliable because they are better maintained, plus operators are less likely to do things which cause their assets to fail. A better understanding of how systems work also means that operators are far more likely to react quickly, confidently and correctly when things do go wrong—a capability which is quite literally priceless, especially in complex, hazardous, tightly coupled facilities.
RCM3 is Effective. Tested. Groundbreaking.
The development of our risk-based RCM, RCM3, started with John Moubray more than 30 years ago and has continued through Aladon Network Members who have helped develop the original concepts and have tested the methodology with many world-class facilities. The results of their pioneering work have been groundbreaking. RCM3 has been implemented successfully with results that exceed the expectations of most. The RCM3 process is much more intuitive and more maintenance decisions are being made by the review groups (people who know the equipment best) more than ever before. Fewer recommendations are referred to upper management for final approval – the RCM3 process is more robust and transparent and our clients love it! RCM3 is the best response to the challenges and expectations brought by the Fourth Generation of Maintenance Management.
RCM3 is now the industry’s most advanced method for managing maintenance and operations to control costs and boost overall productivity. Our aim is to continue to explore new technologies and trends working with our global Network to lead the world with our world-class training courses and robust methodologies.
Understand RCM2 vs. RCM3
A progression table from RCM2 to RCM3 illustrates the extended capabilities of RCM3, which may be viewed here. RCM3 is now the new standard for how organizations manage their operational risks and improve asset integrity.
How Aladon Implements RCM
When it comes to RCM, there is a reason that hundreds of organizations around the world choose Aladon. We have a track record of over 30 years of implementing RCM in every industry on six continents. Because we recognize that implementation is the biggest challenge to the RCM methodology, we offer a step-by-step approach, with a go/no go decision at every stage. The initial process of analysis is the easy part, but it’s in the implementation of RCM that sets Aladon apart.
Implementing RCM often requires changes to existing work processes and tasks that require time and resources to complete. That’s why our approach is to mentor clients through the complete RCM process (planning, scoping, preparation and training, performing, review and audit, implementation and continuous improvement), rather than merely train them. While we know that the benefits of RCM in every industry outweigh the challenges, we nonetheless offer our clients opportunities to opt-out of the process at every stage. This saves them from making large resource commitments and investments upfront.
Following is our systematic approach that has proven our methodology with hundreds of clients throughout the world in every industry:
- Executive Overview: From the start, we spend one day reviewing the RCM process and methodology to an organization’s stakeholders, including: the C-suite, managers, union leaders, program sponsors or anyone who has oversight. The executive overview is focused on the benefits of an RCM-based improvement program and the requirements for successful implementation. From there, the company can decide if they want to proceed.
- Introductory Training: We offer a three-day course with a designated team from the organization, including: engineers, operation managers, maintenance managers, union leaders and subject matter experts. After that, we again offer the organization a go/no go decision.
- Advanced Facilitator Classroom Training: If the organization decides to continue, a select group from the introductory training course joins a 10-day facilitator training program. The facilitator program allows the organization to implement RCM on their own assets using their own people.
- Facilitator Coaching and Mentoring: We assist a select group of the participants from the classroom training group through a pilot project where they analyze equipment they own. This is an onsite process and our experience has shown that the average facilitator delegate will need approximately three weeks of mentoring to be able to work independently. The mentoring and coaching includes activities such as asset prioritization, developing a risk framework, selecting equipment and scoping the analyses, planning the review meetings and audit, and ensuring all the resources are aligned for implementation. Once the classroom training and mentoring period is complete, we perform an onsite evaluation where we determine who has mastered the rigorous RCM3 process and is qualified to become a Certified facilitator.
- Audit, Prepare and Implement results: Together with the facilitator and asset owners, we audit and assist in the implementation of the RCM recommendations. This includes writing detail job plans, developing performance indicators and failed states, optimization of the PM routes, CM prioritization and spare part recommendations.
- Execution and Continuous Improvement: Facilitators work to execute the program with our support, which includes training and mentoring to ensure the team applies the methodology according to our recommendations. Recommendations must be implemented and reviewed periodically.
In addition to this well-developed process, our practitioners typically have at least 15 years of experience. We assign each organization a certified network member with direct experience in their particular industry. The process of RCM is the same in every industry, but we know that industry expertise ensures better results.
There are others who know about RCM. At Aladon, we know what RCM is about.
Ready for proactive maintenance?
The Aladon Network will guide you from reactive maintenance to proactive maintenance. We help companies worldwide optimize their assets, reduce operating and maintenance costs and improve sustainable reliability. Since 1986, our Aladon Advantage offers organizations dedicated service and results-obsessed expertise.
Explore Aladon’s thoughtware or software solutions.